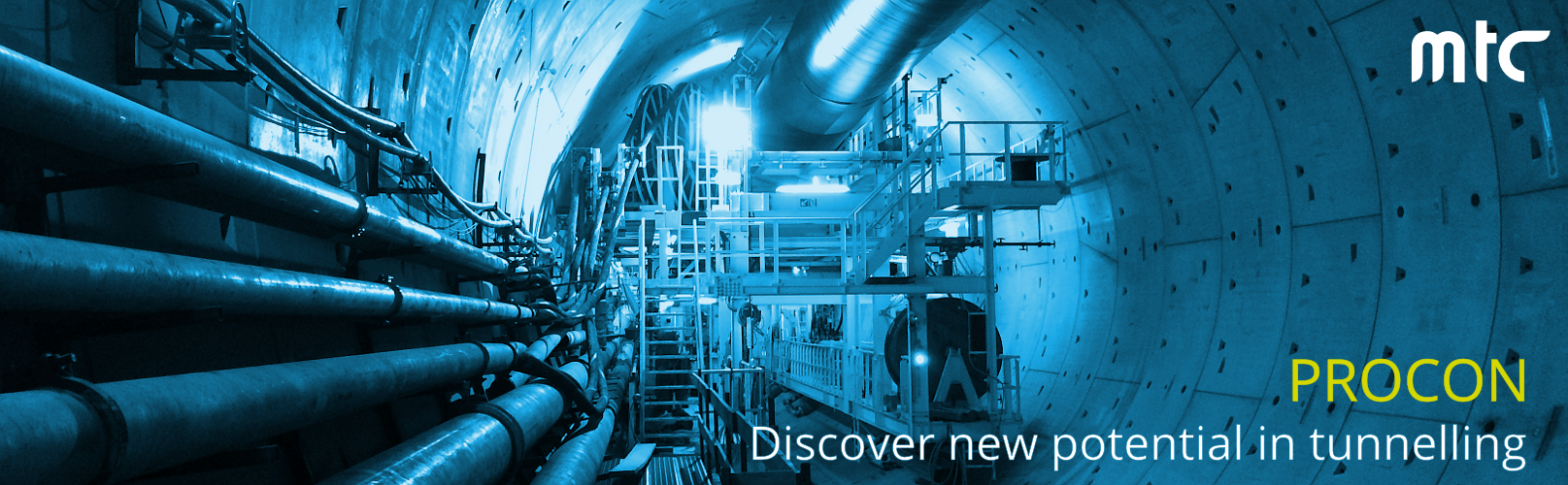
Procon Guide
PROCON II is a software for the
technical controlling of mechanized tunnel drives. A
professional management system for the efficient recording,
analysis and visualization of data. The foundation for your
knowledge management in mechanized tunneling projects. It aims to
visualize time-dependent, location-dependent and object-dependent
data in an intuitive and meaningful way. The figure below shows
the various sources of data and information that can be
integrated, visualized and analyzed in PROCON II.
PROCON II is based on the latest
software technology. Thus, your vast process data are
transformed into visual information. Take advantage of the
affordable possibilities of geographical information systems
(GIS) and link them to your interactive charts. With the generic
chart and dashboard configurator, you can visualize all of the
relevant information tailored to your specific needs and follow
your project live with your web browser.
PROCON II is a web application that is hosted on a
secure and highly availabile cloud system. On the client side,
access to PROCON II is managed by means of SSL encrypted
communication via the HTTPS protocol and an additional access
control layer using personal logins per user. Beside the
installation of a client certificate for the encrypted
communication, no further installation efforts are required on
the client's computer. A special version with an optimized
visualization for mobile devices is optionally available.
The modular design of the software allows to freely configure
the system according to the specific requirements of each
project. Beside the visualization of both real-time and
historical machine data, further information and data can be
integrated to PROCON II. Target values from the design process
can be directly compared to actual measurements. The manifold of
different visualization options can be conveniently arranged on
dashboards and can also be used to create printed reports.
Limit and alarm values are also stored in the system and can be
configured for an automatic alarm messaging in case of breaking
their thresholds.
In addition to sensor values, also
calculated and aggregated values (minima, maxima, averages,
cumulated values, etc.) can be defined used for further analyses
and visualizations. Thus, for example, interactions between
different parameters can be identified and investigated.
Furthermore, it is possible to adapt the database to changes in
the data acquisition that occurs in a later stage of the project
using these customized calculation values without corrupting the
original data.
In addition to the various fields of
application of TBM data, PROCON can also integrate data from
various other data sources related to the tunneling project.
This can include data from the geo monitoring, the separation
plant or the ventilation system. All of this external data can
be assembled on PROCON dashboards along with critical TBM data
to get a holistic overview of the tunneling project.
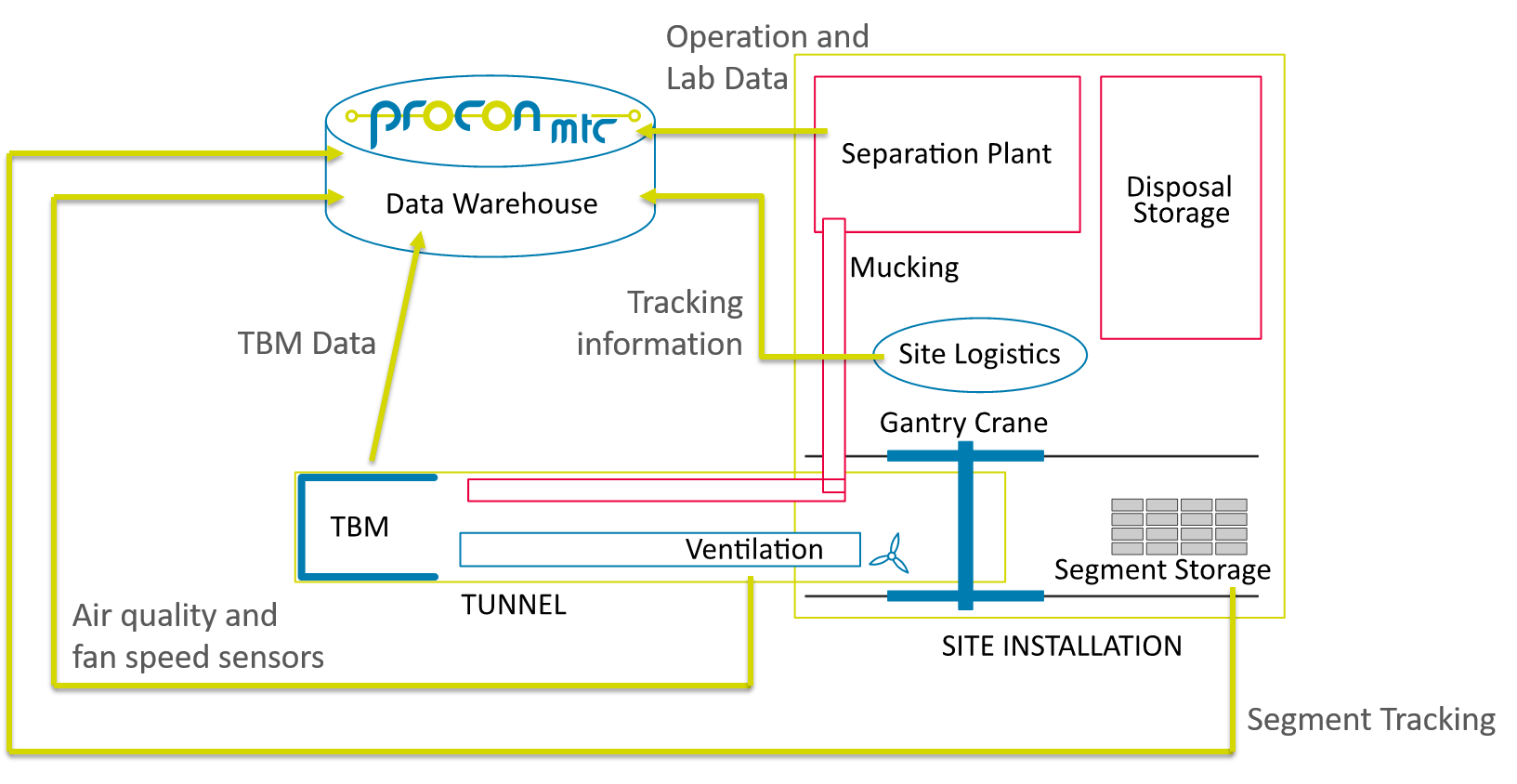
The secured data hosting in a cloud
service computing centre ensures sustainable and secure
archiving of both automatically acquired and manually entered
data. The installation of special hardware on site is not
required. For full usability it is sufficient to set up a
reliable internet connection for the transfer of machine and
monitoring data from site to the PROCON II host.
In the following we invite you to an interactive
introduction tour to PROCON. In this process, the individual
features of PROCON are generally described and assigned to a link
to the software where you directly can test the introduced
features on your own.
Dashboards
All data from the PROCON II data warehouse can be visualized by
means of interactive and customizable charts. These charts can be
directly zoomed, adjusted and arranged on specially developed
dashboards in the browser. These dashboards gather information of
specific topics and are used to display several sources of data
in a common reference system for immediate comparability. In this
context, your data is linked on dashboards with maps of a
geographic information system as well as a digital ground models
in a location or time reference system.
Each chart is
capable of displaying an arbitrary selection of machine data,
target values, additional information and calculated values in a
customizable visual appearance. For this purpose, line charts,
column charts and area charts are available. For suitable data
sources, also pie charts can be employed.
Advanced Analysis
The advanced analysis is a category for more sophisticated dashboards that are accessible for selected users of the system. It is reserved for complex topics, or deeper analyses of certain processes.
Shift Reporting
An interactive module for shift protocols extends the list of
optional features of PROCON. Extracting periods of advance, ring
building and standstill automatically from the machine data,
these time intervals are displayed using a Gantt chart
visualization for each shift.
Shift reporting represents
an essential element of the documentation of a tunneling project.
All actions are documented and can be evaluated as well as
exported. In Procon II, multiple types of shifts per day can be
generated like a morning, day and late shift. The key processes
like advance and ring build are automatically retrieved from the
machine data and assigned to each shift. The reason for each
downtime slot needs to be specified by the user. Here, the
catalog of downtimes is specified according to each project's
requirements. Based on the documented downtime reasons,
evaluations can be performed based on which the process can be
optimized.
For detail evaluations, additional filters on
specific shifts or staff members can be used, hence allowing for
an assessment of reasons for performance differences among the
shifts or to identify specific parameters that correlate with the
performance. The integrative nature of the data warehouse and the
unified temporal and spatial reference system helps identifying
previously unknown interactions and hidden mechanisms in the
process.
Cutter Tool Management
The management of cutter tools is very important especially when
excavating in hard rock. The wear of the individual cutter tools
must be documented to prevent the tunneling machine from being
damaged due to worn-out tools. In Procon II, the individual tools
can be registered and maintained. Data can be entered based on
interventions which represents an event when the cutter tools are
checked for their current wear and changed, if required. Types of
cutting tools like disks, scrapers and buckets are distinguished
in the system and can be managed in respective user interfaces.
The entered intervention data can be displayed using Procon's
chart and dashboard configurators. Here, the tool consumption can
be correlated with machine data and geology information. Thus,
evaluations can be performed of the required tools in context of
the excavated ground. Following the identification of those wear
mechanisms, the prediction of the tool service life can be
improved and maintenance intervals can be optimized, reducing the
risk of unplanned standstills.
Monitoring
In an integrated additional database, monitoring data is stored
that is retrieved from arbitrary instruments registered in the
PROCON II data warehouse. Here, an instrument consists of a
number of data series which contain the individual data. For each
instrument the position and its assignment to a specific class of
instrument (e.g. extensometers or leveling points) is captured.
The data series contain additional information regarding their
assignment to a monitoring section and their warning and alarm
levels which can then be applied to determine the status of the
instrument. Using this information, the location and the time of
measurement of each data entry is connected with the project
reference system.
This allows specific visualization
options for monitoring data. The development of settlement
troughs, for example, can by shown by visualizing monitoring
cross-sections.
Reporting
The documentation of the tunneling process is essential due to
many aspects. Therefore, Procon II offers custom-designed machine
data reports, intervention reports and shift protocols as
printable reports to document the progress. Upon setup of the
project, MTC considers the project-specific requirements and
prepares automatically updating report templates via the web
interface. Reporting periods and various filter functions can be
arbitrarily selected.
The reports can be arranged in
dashboards to allow for adjustments of reporting periods and to
add manual annotations before downloadind and printing them.
Segment Tracking
Segment Tracking describes the consistent tracking of produced
segments throughout their life cycle. This process includes the
production of the segments, their temporary storage on the
construction site, their installation as part of a tunnel ring
and their health status both during construction and operation of
the tunnel. The segments are tracked by applying labels with
codes on each segment.
Maidl Tunnelconsultants offer segment
tracking services in cooperation with a well-experienced partner
company, who provides the workflow implementation as well as all
required hardware including handheld devices for entering the
current information of the corresponding segments and a server
which stores all the collected information and transfers it to
the PROCON server. Thus, segment tracking information is
available and accessible through PROCON at any time.
Ring-based information
In many cases, you may want to add location-based and
process-related additional information. These can be (ranges of)
target values for operational parameters such as the support
pressures. But also external measurements and evaluations such as
ground water levels, information on site logistics, or ground
conditions can be easily acquired on a by-ring basis.
PROCON II enables you to add this data in an arbitrary structure
by means of user-defined processes and definition of respective
data types. These data can be arbitrarily visualized and
combined with machine and monitoring data on Procon's dashboards.
Damage of lining segments is not only possible during production
or in the storage, but also during transport and installation in
the tunnel. It is crucial for quality control to securely
document all damages and to track repair works.
PROCON II
includes an intuitive tool to enter and manage ring damages. Additionally, the
entered damages can be summarized in a PDF report for further
documentation.
Mobile View
Often you are on the move and you have no possibilities to monitor the current status of the project at a computer. Therefore, PROCON II offers a mobile version which can access customized dashboards via smartphone or tablet to monitor different aspects of the project to quickly react in case of problems. You can easily reach the mobile version using the browser of your device and the known URL.
Integration with BIM
BIM can be employed at an early stage of the tunnel project and used already to advantage in the design and construction phases. The key components of these models can be linked to each other by means of a common location and time reference framework.
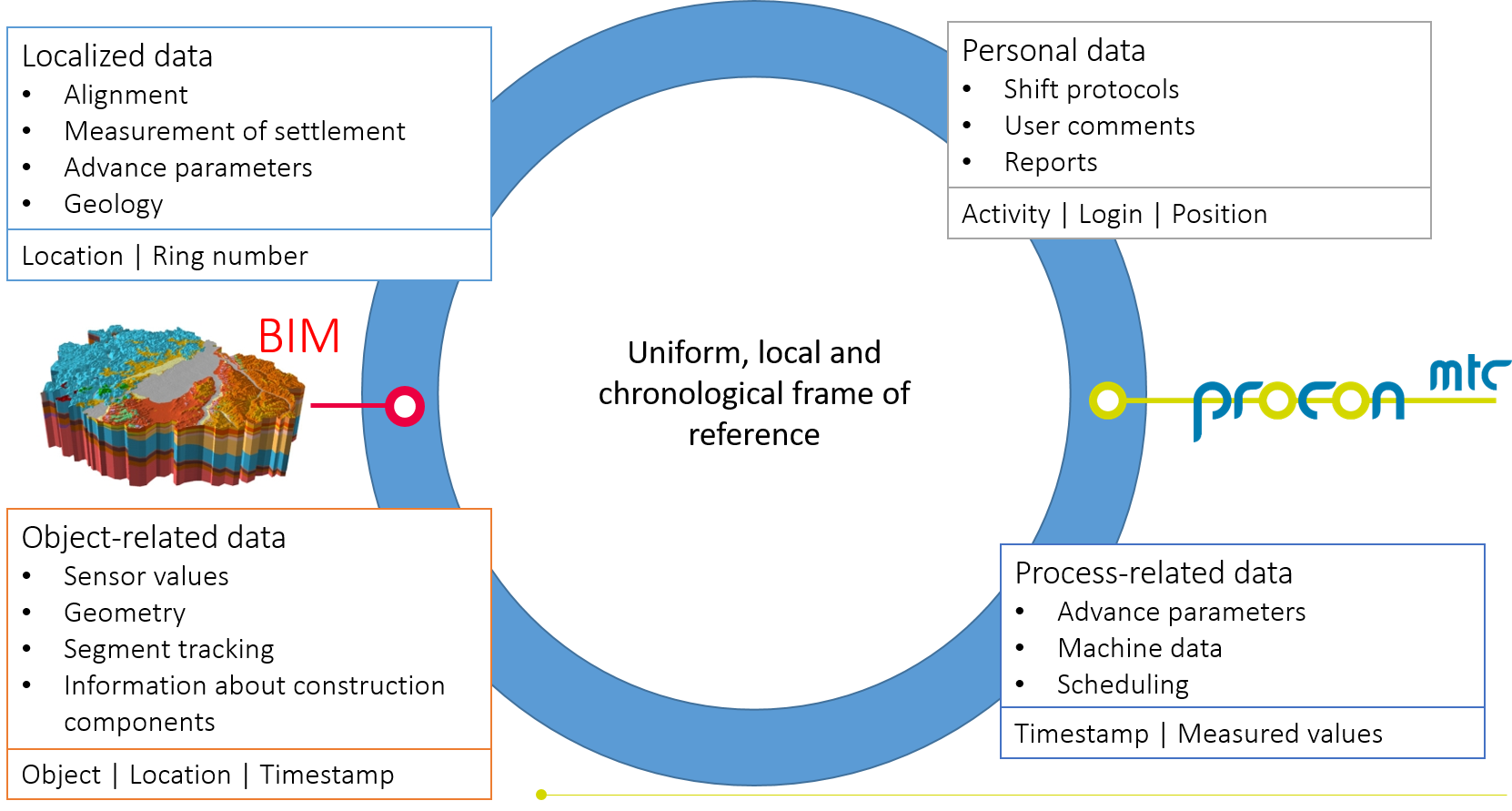
3D tunnel model
The tunnel model consists of the individual segmental linings representing the tunnel tubes. Each tunnel tube contains a number of rings consisting of a defined number of individual segments. Each digital segment has assigned various information from the start like its segment type or its ring number. During the tunnel advance, the information of the segments increases steadily by the incorporation of data from segment tracking and quality management, document linkage or highlighting of the TBM data history (e.g. thrust forces). An easily navigable visualization of the segmented lining allows a quick data identification, problem evaluation and overview of the projects progress.
3D ground model
The purpose of a digital ground model is to provide information
from geotechnical investigation and geological expertise to all
project stakeholders in a computer-readable form.
Incorporating
a 3D ground model into the day-to-day project assessment provides
target-actual comparisons of ground conditions and disposal
masses, the verification of operation parameters and consumption
records as well as conservation of evidence.
The ground
model consists of numerous closed shells representing the
individual ground layers. Each layer has assigned its geological
properties. The volume of the 3D tunnel model is cut out from the
3D ground model. Along its alignment, the tunnel volume is
intersected with the digital ground model to create a digital 3D
tunnel model with areas of similar geotechnical properties.